Taoshi Reduction Gearboxes: Breakthroughs in Antenna Rotary Table Drive Systems
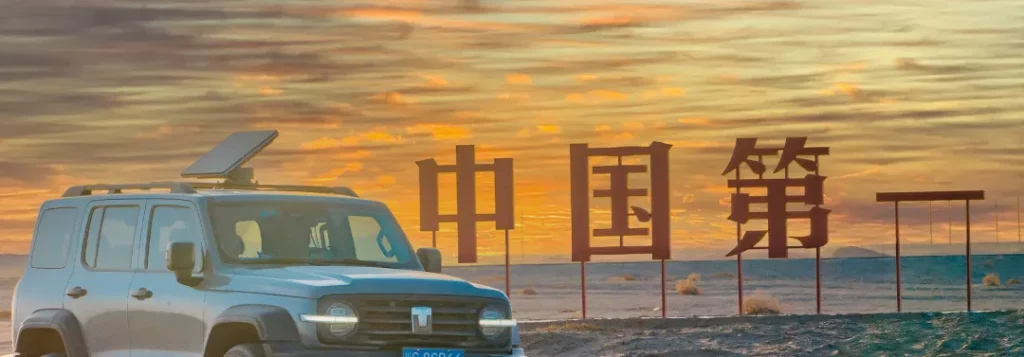
In war, disaster relief, polar research, etc.Extreme scenariosThe antenna turntable is the core equipment for communication, navigation and target tracking. For example, in military operations, the radar antenna turntable needs to be in -40 ℃ to 70 ℃ temperature difference, strong electromagnetic interference environment, to 0.01 ° precision real-time locking high-speed moving targets; in the polar scientific research, the equipment needs to withstand 10 strong winds and salt spray corrosion, to ensure that the satellite signal stable transmission. These scenarios on the reliability of the drive system, environmental adaptability put forward nearlydemanding--Any slight transmission error or mechanical failure may directly or indirectly lead to mission failure or even casualties.The
Battlefield and Disaster Scenes:
Core Challenges of Antenna Turntable Drive Systems
In the context of the escalation of non-traditional security threats (geopolitical conflicts, frequent occurrence of extreme meteorological disasters) and accelerated iteration of polar scientific research equipment, the highly reliable antenna rotary, as the core carrier of satellite communication link construction, radar accurate positioning and emergency signal relay, has become a strategic level equipment to ensure the stability of key information nodes. Its millisecond response capability directly determines the command and scheduling effectiveness and the upper limit of disaster damage control in extreme scenarios, which is specifically manifested as follows:
Satellite communications safeguards
When the fiber optic cable is interrupted and the base station is damaged, the space-based signal transmission relies on the rotary station to accurately track the satellite trajectory, such as in the scene of floods, earthquakes and other large-scale disasters, the satellite rotary system becomes the only communication channel between the disaster area and the outside world.
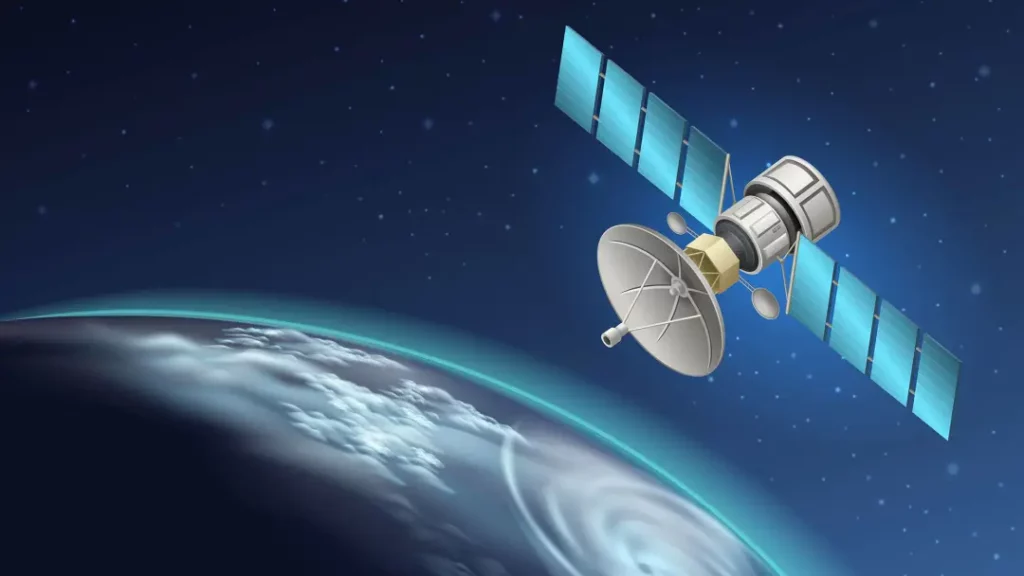
Extreme environments such as polar research
It needs to withstand the harsh working conditions of -50℃ polar low temperature to 70℃ desert high temperature, as well as heavy rain, sand and dust and other extreme climate. For example, in the Antarctic research station equipment needs to be in 60 ℃ temperature difference (-40 ℃ to 20 ℃) under continuous operation, the traditional reducer is easy to lubricant coagulation caused by transmission failure.
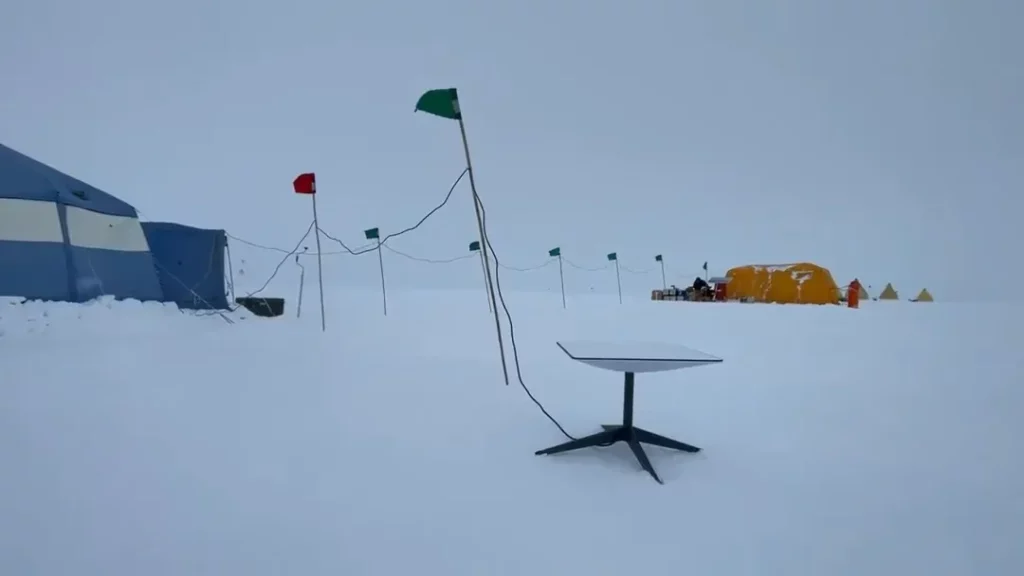
Military grade reliability
Ensure continuous signal locking under the complex electromagnetic environment during wartime, with extremely high demand for signal transmission accuracy and harsh environment in the war zone. For example, when UAV swarms operate together, they need to track targets hundreds of kilometers away in real time through radar antennas, and the transmission system needs to maintain extremely high precision under the low temperature of -40℃ plateau.
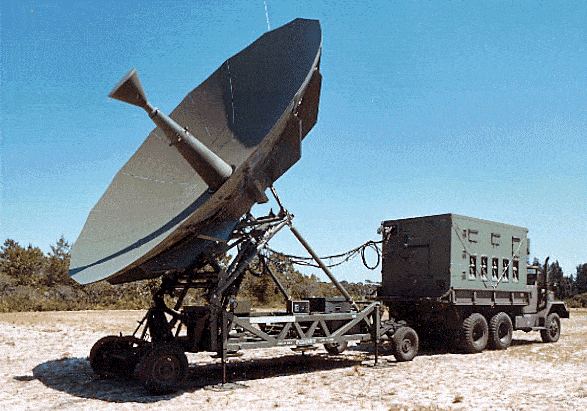
Antenna rotary table core requirements for gearboxes
Antenna turntable core requirements for gearboxes:Precision, Rigidity, Weather ResistanceThe triple challenge
Transmission accuracy
Radar beam pointing error needs to be controlled within ±0.001°, requiring the reducer to return to the difference≤1 arcmin, equivalent to 1/50th precision of the diameter of a hair strand.

Superior impact resistance
Military equipment needs to withstand20G instantaneous impact loadThe gears of conventional gearboxes are prone to chipping and failing, while the torque required to carry the load is extremely high.
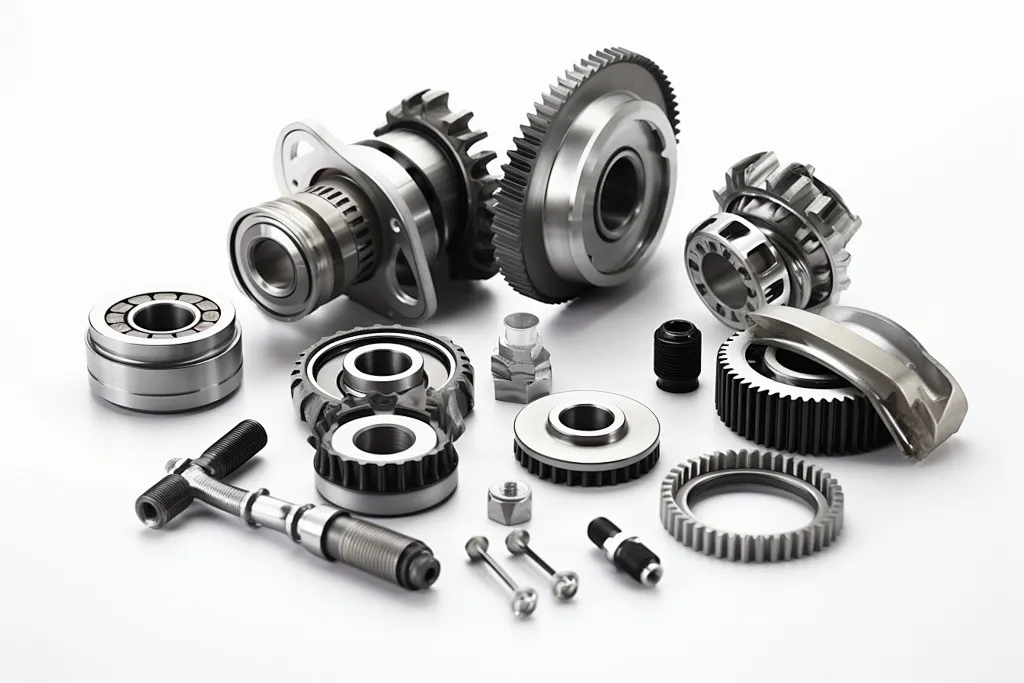
Extreme environmental stability
Polar research turntables require gearboxes in theultralow temperatureIt can be activated under the following conditions and has a salt spray corrosion protection rating up to ISO 9227.
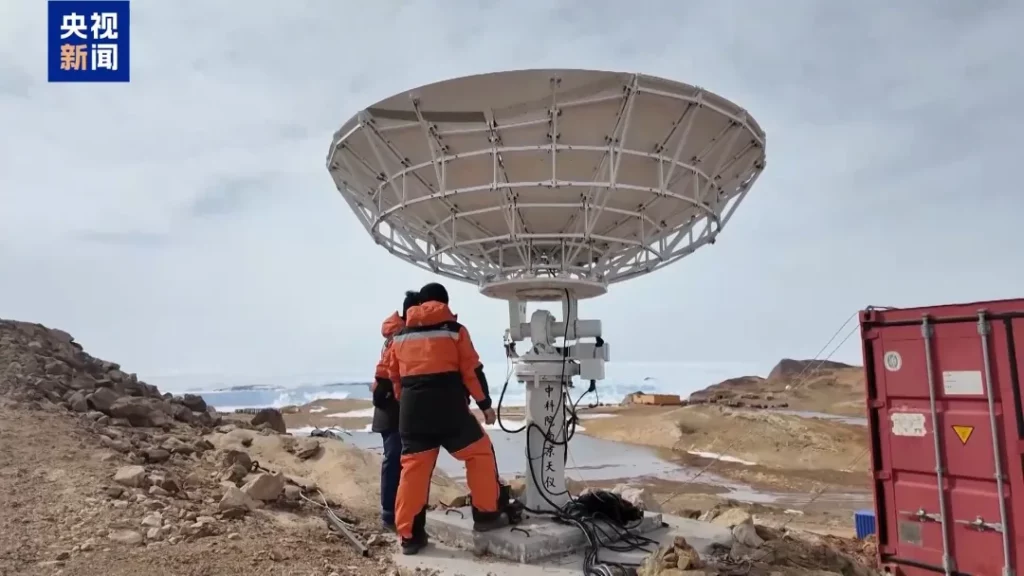
Performance breakout for Taosi reducers:
Explanation of all-weather adaptive technology
Tao Shi ring surface envelope worm gear reducer through the five core technology, to overcome the antenna turntable transmission problems:
Balance of miniaturization and high torque
Circumferential envelope multi-tooth engagement design:Worm and worm gear adopt ring surface envelope multi-tooth meshing design, the number of tooth contact points is more than 3 times higher than that of traditional turbine worm gear, and the torque density per unit volume reaches 500N-M (more than 3 times that of similar products).
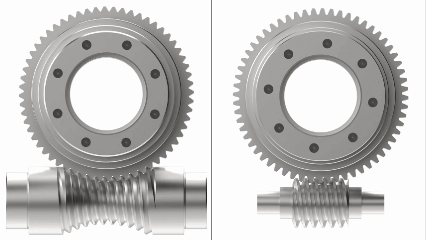
Lightweight materials:Worm wheel and worm gear are made of nitrided alloy steel (surface hardness HV1100), and the shell is made of 7075 aerospace aluminum, which reduces the weight by more than 30% and improves the bearing capacity by more than 100%.
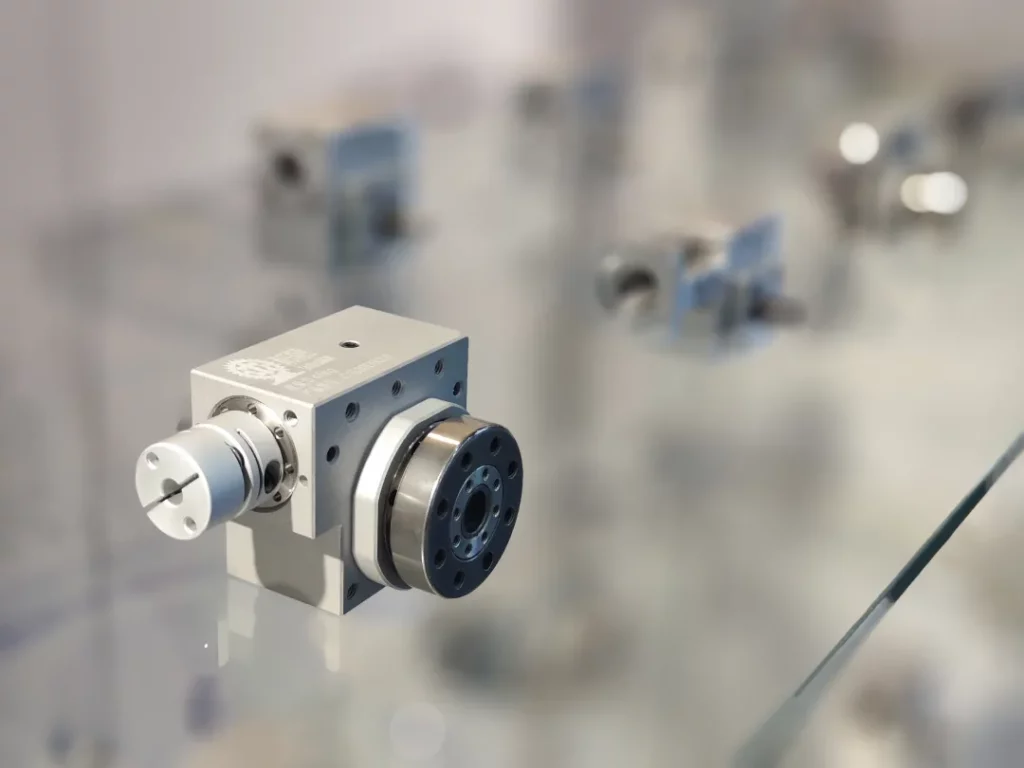
Full temperature lubrication
Adopting high and low temperature resistant grease and IP65 level protection, it can ensure normal and continuous operation even in extremely harsh temperature environments. In the test environment of -40℃~70℃, it can still operate continuously for 10,000 hours and the transmission efficiency remains stable.
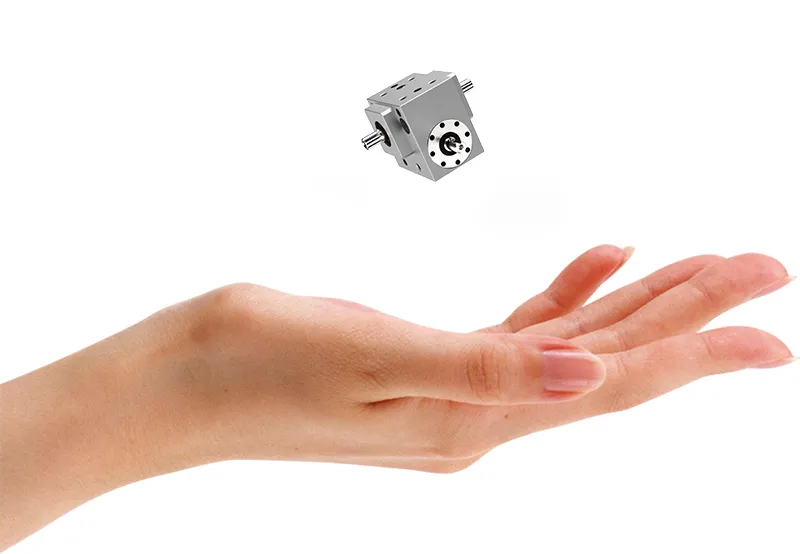
Precision seismic structural design
Adopting ring surface envelope multi-tooth meshing structure, realizing a significant increase in bearing capacity, raw material surface tensile strength up to 1300 MPa, impact resistance up to military-grade standards.

Micro-ring surface envelope technique:
Disruptive breakthroughs in precision drives
Taoshi's original micro-annular surface envelope multi-tooth occlusion technology fundamentally reconstructs the worm gear transmission logic:
Multi-tooth synchronized meshing
The number of teeth in contact with the worm and worm gear is upgraded from the traditional single tooth to multi-tooth, which results in a more uniform load distribution and an instantaneous impact load capacity of 3000N-M.
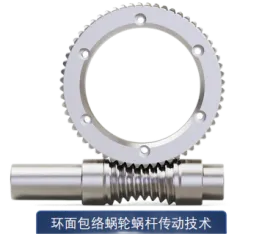
Nano-scale surface treatment
Using self-developed processing grinding machine for processing, its gearbox processing accuracy is as high as 0.005mm, processing efficiency is shortened from 8 hours to 20 minutes, and the surface finish is up to 0.2μm.
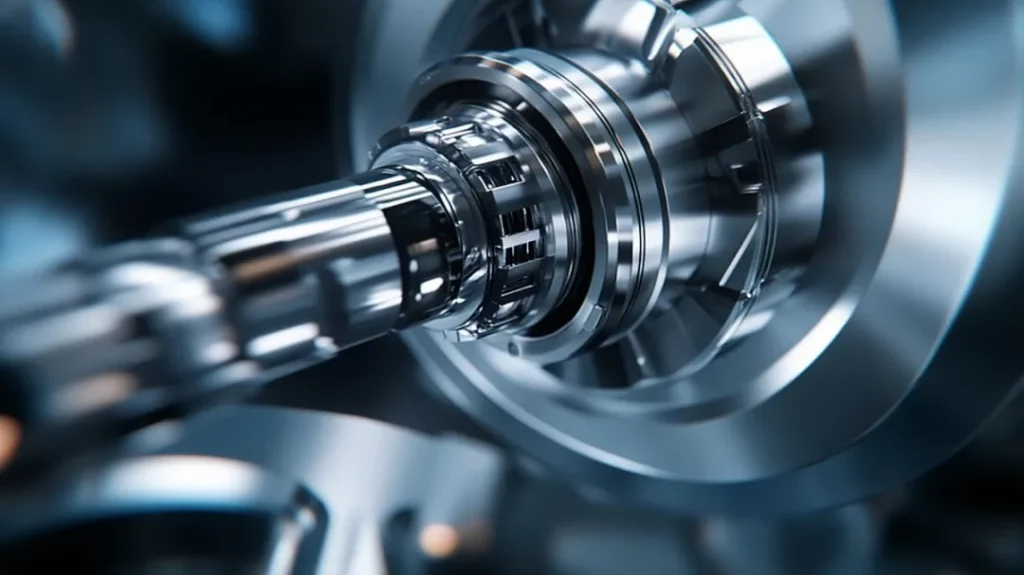
highly accurate
Under the application scenario of high-end demanded precision, it realizes ±0.5 arc-minute precision control, and achieves long-lasting target tracking and locking.
