10 years to overcome the "neck" technology: Chinese engineers of the speed reducer breakthrough battle
I. Background to the breakout: the technological dilemma of being blocked for 30 years
- Japanese monopoly and market suppression
Since the 1990s, Japanese companies to RV reducer and harmonic reducer as the core, occupying more than 80% share of the global industrial robot reducer market. Through the "technology blockade + price dumping" strategy, the long-term suppression of the development of local enterprises in China - when the Chinese enterprises R & D breakthroughs, Japanese enterprises immediately reduced prices 30%-50%, resulting in the loss of cost competitiveness of domestic reducers.
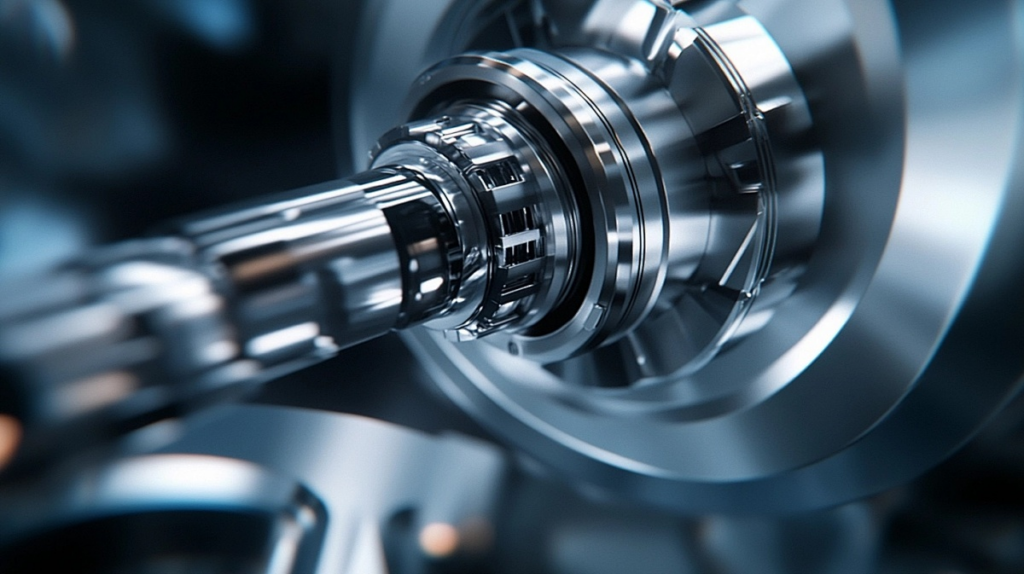
- The fatal shortcomings of domestic industrial robots
Reducer as one of the three core components of industrial robots (accounting for more than 35% of the cost of the machine), and its accuracy directly determines the stability of the robot arm action. 2015 years ago, the life of the domestic reducer is only 3,000 hours (Japanese products up to 20,000 hours), and the gap in the precision of the return difference of more than 3 times. This leads to domestic industrial robot market penetration rate of less than 10%, high-end areas are completely dependent on imports.
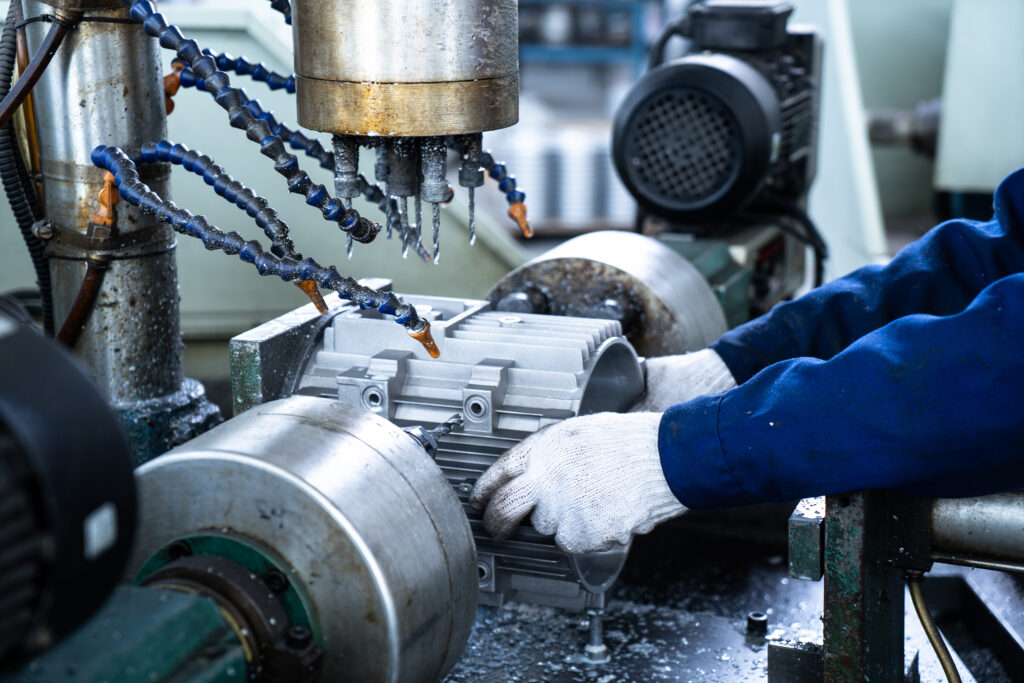
II. Technology attack: the 10-year long march from laboratory to industrialization
- Gear Shaping Breakthrough by Zhang Yueming's Team
Prof. Zhang Yueming's team at Beijing Institute of Technology has overcome the core problem of RV reducer through dynamic meshing theory model and gear trimming technology:
- Reduced the transmission error from ±0.02° to ±0.001°, reaching the top international level;
- The service life exceeds 15,000 hours, and the gear wear problem is solved by composite ceramic coating technology.
Bending the Curve in Tausch Ring Surface Envelope Technology
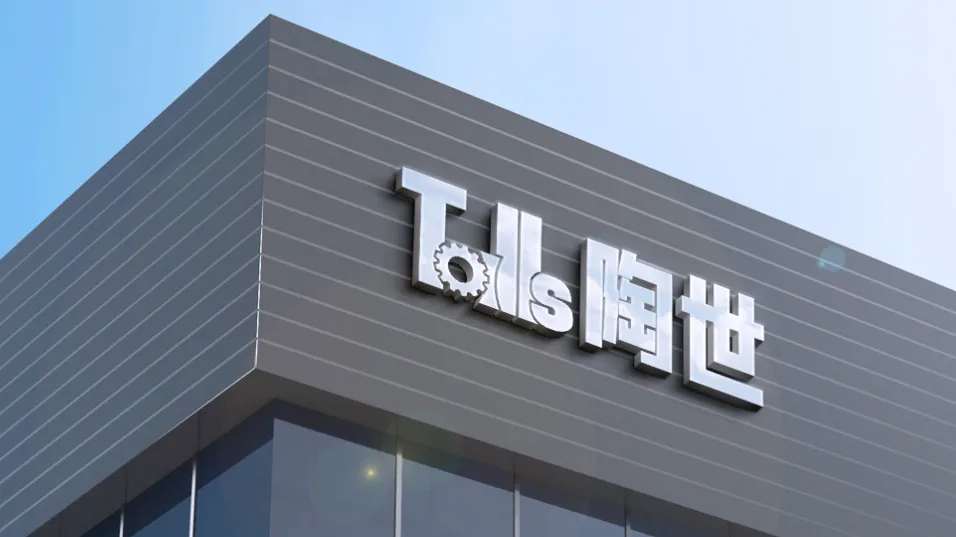
Taoshi engineers took a different approach to develop miniature ring surface envelope multi-tooth gearboxes:
Adopting worm gear multi-tooth synchronous meshing design, the contact area is increased by 6 times, and the torque density reaches 500Nm/Kg;
Made of special steel, the tensile strength is up to 1300 MPa, which is more than 3 times of the common worm gear reducer in the market.
Machining with self-developed machining grinder, its reducer machiningAccuracy up to 0.005mmProcessing efficiency from 8 hoursReduced to 20 minutesSurface FinishUp to 0.2μmThe
The Taoshi reducer housing is made of7075 aviation gradeHigh-strength aluminum, worm gears and worm gears are made of special steel through a series of technological treatments, combined with uniqueCircumferential Envelope DesignThe overall weight of the reducer is reduced by about 30% while the torque is guaranteed.
In the high-end demand for precision application scenarios to achieve ± 0.5 arc minute precision control, breaking the monopoly of Japanese companies in the field of miniature high-precision reducer.
And miniature ring surface enveloped worm gear reducer, with its own 90 ° drive, self-locking and other properties, more and more are used in all kinds of high-precision industry.
- collaborative innovation of industry chain
Material side: cooperating with large state-owned enterprises to develop high strength and toughness alloy steel, gear fatigue strength increased by 40%;
Manufacturing end: Self-developed nine-axis machine tools, machining efficiency increased by 70%, cost reduced by 80%;
Detection end: establish a full life cycle accuracy monitoring system to realize 0.1 arc graded online calibration.
- Breakout results:
Rewriting the global industry landscape
- Market share reversal
In 2024, the domestic market share of domestic speed reducer jumped from 10% to 35%, forcing Japanese enterprises to reduce the price of similar products by 25%.
- High-end breakthroughs
Aerospace: Taoshi cooperates with many enterprises, such as Aerospace Science and Industry, and the reducer is applied to the key transmission structure of high-precision automation, special robots, and geospatial satellites, realizing high-precision transmission and high-rigidity self-locking.
Medical instruments: provide transmission support for domestic surgical robots, with instrument operation error less than 0.01mm;
Humanoid robot: a well-known domestic robotics company, with joints made of Dow products and dynamic load capacity upgraded to 200%.
Dexterous hand: Tao Shi self-developed full-drive dexterous hand joint module, to realize the world's highest degree of freedom (20 degrees of freedom) dexterous hand, and keep the maximum grip strength of the whole hand up to 20kg, accuracy of ± 0.015mm.
Military: Its operating noise is lower than 60 dB, which can effectively reduce the interference to the working environment.
- Implications and Prospects
Core logic of technological self-reliance
Professor Zhang Yueming has frankly said, "The breakthrough of reducer is not a single point of innovation, but a systematic reconstruction from materials, design to manufacturing process." This requires deep synergy between industry, academia and research. Such as Tao Shi and the Shenzhen Institute of Advanced Technology of the Chinese Academy of Sciences school-enterprise cooperation, the theoretical model of the university quickly into the production line process.
concluding remarks
This 10-year breakthrough war, not only to break the "make better than buy" myth, but also verified the Chinese engineers "systematic innovation" ability. As the great master craftsman Cheng Ping in the field of welding breakthrough revelation: "the breakthrough of the necklace technology, the need for ten years of day-to-day focus, but also the need for interdisciplinary, cross-industry cooperation." In the future, China's high-end manufacturing will usher in a new golden age.
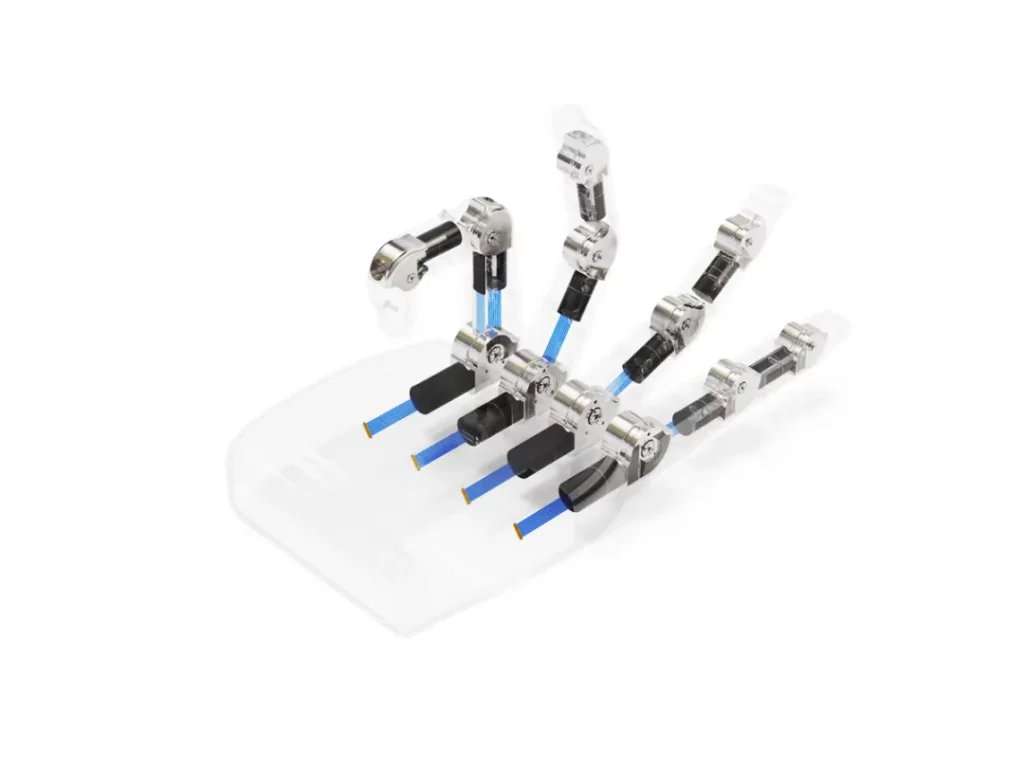